fig7
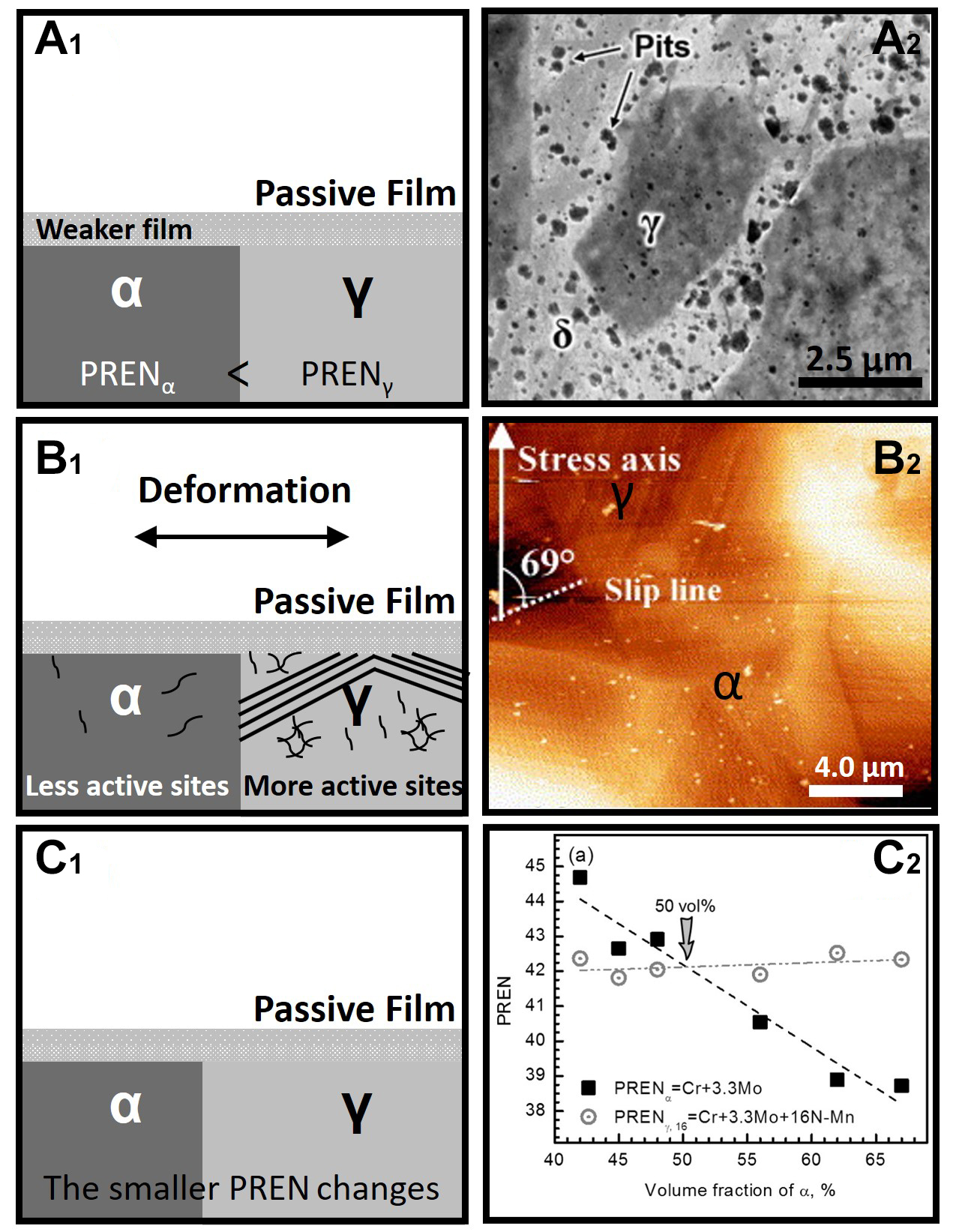
Figure 7. Summary of the studies on the pitting corrosion resistance between ferrite and austenite. (A1) The pitting resistance equivalent number of the ferrite phase is smaller than that of austenite. Therefore, the passive film of ferrite is unstable, and pitting corrosion occurs preferentially in ferrite. (A2) In the chloride-containing environment, the amount of pitting corrosion initiated in the ferrite phase is significantly more than that in the austenite phase[28] (Open Access) (B1) Under plastic deformation conditions, austenite forms more dislocation walls, slip bands, and dislocation outcropping defects. Therefore, more active sites appear on the surface of the austenite phase, and the pitting corrosion resistance gap between ferrite and austenite becomes smaller and even reversed. (B2) After plastic deformation, the defects in austenite increase significantly, whereas that in the ferrite phase changes little. (Reproduced with permission[83]. Copyright 2006, Elsevier). (C1) Element diffusion occurs during the heat treatment process to change the phase ratio. The minimum value of the pitting resistance equivalent number changes, and the pitting corrosion resistance of duplex stainless steel changes. (C2) UNS S32750 with different phase ratios exhibits different pitting potentials. (Reproduced with permission[23]. Copyright 2015, Elsevier.