Advancing strategies on green H2 production via water electrocatalysis: bridging the benchtop research with industrial scale-up
Abstract
Water splitting provides clean hydrogen via different technologies such as alkaline water electrolysis, proton exchange membrane electrolyzers, solid oxide electrolysis cells, and photoelectrolysis, each with advantages and challenges. The focus on alkaline water electrolysis highlights its maturity compared to emerging methods. Non-noble metal catalysts offer increased stability, low cost and operational lifespan. Challenges such as low current density, gas crossover, corrosive electrolytes, and limited efficiency are still to be addressed. These advanced electrocatalysts are summarized for alkaline oxygen and hydrogen evolution reactions. Meanwhile, different factors including product gas bubble management, operation conditions, separator and electrolyte affecting the performance were concluded and discussed. For the promising approach, seawater splitting is still far from large-scale application. Salinity, pH fluctuations, and complex composition are significant obstacles. The review underscores the need for improvements in electrocatalysts to enhance the efficiency, stability, and practicality of water splitting for hydrogen production, ultimately contributing to the growth of the clean hydrogen market and supporting the transition to sustainable energy systems.
Keywords
INTRODUCTION
To achieve net-zero emissions and accommodate the escalating need for renewable energy sources, hydrogen produced from renewable energy emerges as a pivotal force in diminishing reliance on fossil fuels, thereby fostering economic and environmental sustainability[1-9]. The significance of hydrogen spans a spectrum of fields, profoundly influencing the electricity system, energy storage, transportation, industrial processes, and gas grids [Figure 1A][10-14]. Notably, it serves as a crucial reservoir for surplus electricity generated from renewable sources, effectively harmonizing supply and demand dynamics. Its widespread application stems from its exceptional properties, supporting diverse functions such as ammonia production, petroleum refining, steel manufacturing, and the electronics and semiconductor sectors[1]. The burgeoning global demand for clean hydrogen has led to a remarkable upsurge in the market size. From its valuation of 1.41 billion USD in 2021, it is expected to exceed 5.95 billion USD by 2030, demonstrating a substantial annual growth rate of 17.36% within the forecast period from 2022 to 2030 [Figure 1B][15]. This expanded market size opens doors to abundant opportunities for various communities and fosters stronger relationships among policymakers, industry practitioners, and evaluators.
Figure 1. (A) Five fields affected by the green hydrogen. (B) The global clean hydrogen market size was valued at USD, estimated from 2021 to 2030. The data is collected from ref[15]. (C) Overall hydrogen evolution reaction mechanism including Volmer, Tafel and Heyrovsky steps. (D) Oxygen evolution reaction mechanism in an alkaline environment.
Water splitting for hydrogen generation represents a promising avenue for large-scale hydrogen production[16,17]. Various technologies, such as photocatalysis[18-22], alkaline electrocatalysis[10,23], proton exchange membrane (PEM) electrolyzers[24], solid oxide electrolysis cells (SOEC)[25], and photoelectrolysis[26,27], offer distinct approaches to this process, each with its advantages and limitations [Table 1]. Solar-driven hydrogen evolution can transfer solar energy to chemical energy directly but is still limited by the relatively low efficiency because of the high photogenerated charge recombination rates. Therefore, further development and refinement are required to address limitations and unlock their full potential for efficient and cost-effective hydrogen production. For example, PEM electrolysis with noble metal catalysts exhibits high performance and good anti-acid corrosion, but the relatively short durability of its membrane and expensive catalysts make it costly for widespread applications[28,29]. The SOEC and photoelectrolysis encounter significant hurdles due to the harshly corrosive environment and engineering complexities, such as high operating temperatures or low energy efficiency. These challenges pose obstacles to their practical implementation at a large scale[29]. Alkaline water electrocatalysis currently stands as a mature technology with reasonable efficiency compared to other emerging methods. It has been commercialized for several decades. Alkaline water electrolysis (AWE) is processed in an aqueous solution of NaOH or KOH with a concentration of 20-40 wt.% at a temperature range of 70-90 °C. Non-noble metal catalysts are used in alkaline water splitting, which differs from PEM relying on the platinum group metals. The operational lifespan of a commercial AWE can be over several years. These merits distinguish it from PEM electrolysis and make it easier to scale up[23]. However, it also faces challenges such as low current density due to the high impedance of the electrolyte and diaphragm, the crossover of gases leading to gas impurity and unsafety, corrosive electrolyte, and low efficiency[23].
Comparison of main parameters for different water splitting cells
Parameters | AWE | PEM | SOEC | Photoelectrolysis |
Efficiency | 60%-80% | 60%-80% | 40%-60% | 2%-12% |
Current density/ | 100-400 | 500-2,000 | 300-1,000 | |
Catalysts | Ni-based catalysts | Pt group-based catalysts | Perovskite lanthanum strontium manganese | SrTiO3 based catalysts |
Electrolyte | 20-40 wt.% KOH | Nafion membrane | ZrO2/Y2O3 | Water |
50-80 | 50-80 | 600-900 | ||
Advantages | Cheap catalysts; long-term stability | High current density | High efficiency; low cost; long-term stability | Green energy conversion |
Disadvantages | Low current density | Expensive catalysts; short durability of membrane | Corrosive operating environment; high temperature | Low efficiency; ineffective catalysts |
The water splitting process comprises the anodic oxygen evolution reduction (OER) and the cathodic hydrogen evolution reaction (HER). For OER, the most efficient catalysts are Ir/Ru-based materials[30-32], while Pt-group metals are used for HER[33,34]. However, these catalysts composed of noble metals are both rare and costly. Consequently, the widespread implementation of water splitting based on these noble metals has been impeded. The alkaline HER involves two primary reaction mechanisms, namely Volmer-Tafel and Volmer-Heyrovsky mechanisms [Figure 1C]. Key intermediates, such as adsorbed H*, OH*, and H2O*, largely dominate the reaction pathways in this process[10]. In acidic HER, the hydrogen binding energy theory (utilizing the hydrogen-adsorption ability-activity volcano plot) is often applied to explain reaction origins. This is different from the alkaline HER, where slow kinetics are influenced by multiple factors[13], including the sluggish transport rate of OH- and the challenging cleavage of the O-H bond in water, resulting in kinetics approximately two orders of magnitude slower compared to that in acidic conditions[14]. Moreover, the alkaline OER involves multiple steps with the participation of electrons and protons [Figure 1D]. The reaction may occur via a sequential mass transfer via OH- → OH* → O* → OOH* → O2 + * (*indicates the catalytically active site on the catalyst surface)[10,13]. Establishing a suitable descriptor for alkaline OER and understanding the structure-performance relationship remain complex challenges. Various theories, such as metal bond energy with OH, the number of d electrons, electron occupancy in the eg orbitals, the adsorption energy difference between ΔGO* and ΔGOH* (binding energy of O* and OH*), and the crystal lattice oxygen mechanism, have been proposed to comprehend this
In laboratory research, parameters such as Tafel slope, Faradic efficiency (FE), overpotential (η), turnover frequency (TOF) and stability are used as key criteria for catalyst evaluation[13,14]. These can even provide standards to compare the different catalysts. In electrolysis, η describes an extra potential or voltage required to drive the reaction but beyond the standard thermodynamic potential. Higher η leads to reduced efficiency and higher costs. Catalysts exhibiting lower η can achieve heightened current density at lower potentials. A frequently utilized η value concerns the attainment of a current density of 10 mA cm-2 (referred to as η10). It is important to note that η10 is influenced not only by the intrinsic characteristics of the catalysts but also by working conditions, loading mass, and the exposed active area. TOF measures the rate of converting reactants into hydrogen or oxygen per active site per second at a specific potential. It stands as a critical metric for evaluating the effectiveness and reaction kinetics of an electrocatalyst. Yet, accurately determining the number of active sites remains a significant challenge. FE represents the ratio between the generated hydrogen or oxygen and the theoretically estimated quantity of gases derived from the applied electrical charge. Any by-products formed in the system contribute to Faradaic losses and escalate the overall cost. The Tafel slope, extracted from the linear sections of the Tafel plot correlating the logarithm of current density with overpotential, serves as a tool to identify the kinetics study and potential reaction mechanisms. For instance, distinct Tafel slopes of 29, 38, and 116 mV dec-1 suggest the Tafel, Heyrovsky, and Volmer steps as rate-determining steps for HER. Long-term application viability relies significantly on stability[10]. Accelerated cyclic voltammetry (CV) and chronopotentiometry or chronoamperometry tests are employed for stability assessment. A marginal enhancement of η after numerous CV cycles indicates favorable stability. In chronoamperometry testing, it is recommended to conduct tests at higher fixed current densities, such as 100 or 200 mA cm-2. Besides, similar parameters are used to describe industrial production, such as cell efficiency and voltage. These are related to the lab parameters but not totally the same. It is noted that 1.23 V is the equilibrium voltage for the reaction. However, the operational cell voltage is much higher than that because of the ohmic loss originating from the resistance of the electrolyte, separator, gas bubble effects, and so on[11]. For the efficiency of water electrolysis, several parameters depend on the different electrolysis systems. For example, it can be valued by the production of hydrogen against the total electrical energy consumed by the system or by calculating the net efficiency, denoted as ηH2 production rate and ηnet efficiency[23]. These parameters are affected by different factors in industrial production.
In this review, we summarize different factors that exert an impact on the overall cell efficiency not only in laboratory conditions but also for large-scale production. Different from the experiments in the laboratory, industrial production can be significantly influenced by the cell configuration, which leads to different product collections and electrolyte supply. Electrolyte and separator engineering is another field that does not attract enough attention from researchers. For providing conductivity between the cathode and anode, they bring great ohmic loss in this reaction, leading to reduced efficiency. The intrinsic performance of catalysts is the key point for this process. However, the research on high-rate and long-term stability is still insufficient. Lastly, bubble management can dominate the efficiency loss in industry, which has attracted growing attention. This review aims to bridge the gaps between laboratory studies and industrial practice. It emphasizes the importance of directing attention and investment toward addressing these issues to advance practical applications.
ELECTROCATALYTIC CELLS
The configuration of electrocatalytic cells for large-scale hydrogen production differs significantly from the cells used in laboratories. In industrial applications, two types of commercial devices are widely used, as shown in Figure 2: the conventional alkaline water splitting electrolyzer (AWE) and the anion exchange membrane (AEM)[1]. In the case of the AWE [Figure 2A], a microporous diaphragm serves as a separator for the anode and cathode immersed in an electrolyte of 30-40 wt.% KOH[29]. The diaphragms are made of materials including inorganic ceramics such as asbestos, potassium titanate, or various polymers[35]. The operation current density is around 400 mA cm-2, with a cell voltage range of 1.85 to 2.2 V. Operating temperatures usually range between 70-90 °C, with conversion efficiency reaching up to 60%-70%[28]. Key advantages of AWE include its low cost and excellent stability due to the non-precious electrodes used. However, the AWE setup faces challenges such as a significant gap between the cathode and anode, coupled with high-resistance diaphragms (approximately 4 Ω cm-1 at 30 °C), contributing to increased ohmic overpotentials in the cell. Furthermore, the susceptibility of KOH electrolyte to reacting with CO2 in the ambient air generates carbonate, leading to reduced OH- concentration and ionic conductivity of the electrolyte. The deposited K2CO3 can also obstruct ion transfer channels in the gas diffusion layer. These challenges influence the efficiency and long-term performance of the AWE system.
Figure 2. (A) Conventional alkaline water splitting electrolyzer. (B) Anion exchange membrane electrolyzer. (C) Capillary-fed electrolysis cell[36]. Copyright 2022, The Authors, published by Springer Nature.
Over the past few decades, a superior commercial application known as AEM [Figure 2B] has been developed and implemented due to its cost-effectiveness and high activity[1]. This system utilizes an anion exchange membrane (such as OH-) functioning as a solid electrolyte and gas separator. This membrane is positioned between anode and cathode films, forming the membrane electrode assembly (MEA). Hydrogen gas evolves by circulating pure water or a low concentration of alkaline aqueous solution through the cathode side, while hydroxyl ions diffuse through the AEM to the anode side for oxygen production. The AEM configuration features a compact cell structure and lower ionic resistance due to the MEA. However, the confined area between the thin film and AEM limits the mass loading of catalysts. At higher current densities, excessive gas bubbles formed on the electrodes can impede access to the surface of catalysts by the water/alkaline solution, hindering subsequent reactions. A novel concept recently introduced in water electrolysis is the capillary-fed electrolysis cell [Figure 2C][36]. In this design, hydrogen and oxygen gases are both collected in the gas chambers, avoiding the bubble effect and causing decreased efficiency. The electrolyte is continuously drawn up from the separator using a capillary effect from the electrolyte reservoir at the base of the cell. Remarkably, this design exhibits a cell voltage of only 1.51 V at 0.5 A cm-2 and
The substantial differences between commercial applications and laboratory studies can cause notable disparities in the performance of devices. In commercial applications, the migration of gas bubbles produced on the electrode surface significantly influences gas impurities and the activity and stability of electrodes [Figure 2][37,38]. Under high-rate operation (i.e., current density > 400 mA cm-2), a substantial volume of gas bubbles forms on the electrode. If these bubbles nucleate and coalesce without detaching from the electrode surface, they can reduce surface energy, potentially covering active sites. Continual accumulation of gas bubbles on the electrode surface can pull the electrolyte away from the electrocatalysts, leading to a significant ohmic drop and energy loss in the electrolysis process[39]. When these large bubbles detach from the surface, the abrupt disturbance of the electrolyte may cause nanostructural collapse and the loss of catalysts on the interface, reducing the stability and activity. To overcome these negative effects, various bubble manipulation strategies have been proposed. For instance, methods involve superhydrophobic modification by nanostructuring to prevent a flat surface, 3D electrode creation with gas channels, and electrolyte component adjustment. These approaches aim to prevent the formation of large bubbles, promote their removal, and mitigate the associated adverse effects[40].
ELECTROLYTE AND SEPARATOR
Alkaline water splitting commonly employs an aqueous KOH solution. Various factors related to the electrolyte composition play vital roles, including conductivity, gas solubility, gas diffusion, and viscosity[41,42]. Typically, KOH solutions with a concentration of 5~7 mol L-1 (corresponding to 25-30 wt.%) demonstrate the highest conductivities compared to other alkaline metal bases at the same concentration. Notably, the electrolyte concentration significantly influences gas diffusion and solubility[42]. Since the presence of hydroxide ions notably decreases oxygen solubility, it brings an advantage in preventing gas crossover KOH solution concentrations[43]. Meanwhile, efforts on electrolyte engineering to enhance the whole cell efficiency and reduce cost have also been reported. For example, the trace of impurities in the electrolyte can affect the stability of the catalysts[44]. Also, the implementation of electrolyte engineering can accelerate the detachment of gas bubbles on the electrode and reduce the electron transfer barrier between the electrolyte and electrode at high current density. One of the potential methods is adding surfactants in the electrolyte to reduce the surface tension so that the critical size of the bubble at detachment can be decreased[11]. However, the impact of the surfactant on conductivity, stability and efficiency can be studied and evaluated.
Separator is another important part of AWE. Porous separators, such as diaphragms, are used to separate the oxygen and hydrogen gas evolved in the anodic and cathodic compartments and provide the ionic transfer channel. Therefore, porosity and wettability are important factors related to gas separation and conductivity. Since the working environment is corrosive and pressured, the separator should possess high chemical durability and mechanical stability. Inorganic separators are generally used in alkaline water splitting for their high anticorrosive properties. Asbestos is efficient and cheap, but it is not an ideal separator for its drawbacks. For example, the poor conductivity will reduce the ionic conductivity. The toxicity of microfibers can lead to serious lung diseases such as cancer and pneumoconiosis[45]. The porous ceramics are used for excellent wettability and stiffness. The typical separator is a flexible porous zirconia (ZrO2)-based porous thin membrane, Zirfon[46], which is highly chemically stable and low resistant. The combination of ZrO2 and polysulfone matrix led to good wettability and low gas permeability. With these properties, Zirfon shows great potential for the industrial alkaline water splitting process[47].
CATALYSTS
The catalyst plays a critical role in the entire electrolyzer system due to its impact on efficiency, stability, cost, and preparation methods. While Ir/Ru-based oxides and Pt group metals exhibit outstanding performance in water splitting, their limited availability poses challenges for large-scale applications due to high costs. To ultimate the noble metal utilization and increase efficiency, single-atom catalysts were developed. They exhibit appealing performance because of the well-defined active site configuration and unique electronic structures[48]. In industrial production, nickel mesh/foam serves as the primary electrode material. Transition metal-based materials such as Ni, Co, and Fe demonstrate competent performance and stability at a more affordable cost. This section summarizes recent research focused on transition-based catalysts in alkaline water splitting [Table 2].
Summary of the OER and HER performance of the electrocatalysts
Catalysts | Electrolyte | η10/mV | Tafel slop/mV dec-1 | Stability | Ref. | |
OER | α-Ni(OH)2 | 0.1 M KOH | 331 | 42 | 100 CV cycles | [49] |
CoTe2 | 0.1 M KOH | 357 | 32 | 2,000 CV cycles | [50] | |
α-MnO2 | 0.1 M KOH | 490 | 77.5 | - | [51] | |
α-Fe2O3 | 1 M NaOH | 317 | 58.5 | 30 h | [53] | |
Ni3S2/NF | pH = 14 | 260 | - | 200 h | [54] | |
Co3O4-Vo | 0.1 M KOH | 300 | 68 | 2,000 CV cycles | [56] | |
NiFe-LDH | 1 M KOH | 230 | 77 | 36 h | [58] | |
NiFe-LDH | 1 M KOH | 269 | 48.3 | 6,000 h | [61] | |
HE-LDH | 1 M KOH | 213 | 27.5 | 700 h | [63] | |
HE-LDH | 1 M KOH | 218 at 50 mA cm-1 | 47.1 | 600 h | [64] | |
HE-LDH | 1 M KOH | 259 at 100 mA cm-1 | 49.0 | 1,000 h | [65] | |
CoP | 0.1 M KOH | 250 at 20 mA cm-1 | 66 | 1,000 CV cycles | [66] | |
Co4N | 1 M KOH | 257 | 44 | 1,000 CV cycles | [67] | |
HER | Ni dendrites | 6.0 M KOH | 160 | 102.7 | 2,000 CV cycles | [68] |
MoNi4 | 1 M KOH | 15 | 30 | 2,000 CV cycles | [71] | |
CoSn2 | 1 M KOH | 103 | 78 | 14 h | [73] | |
NiMoCo | 1 M KOH | 13.7 | 70.64 | 120 h | [76] | |
Co2P | 1 M KOH | 171 at 20 mA cm-1 | - | 1,000 CV cycles | [83] | |
Ni5P4 | 1 M KOH | 13 | 50 CV cycles | [84] | ||
NiS2 | 1 M KOH | 80 | 135 | 90 h | [91] |
OER catalysts
Hydrogen is produced via HER, a component of the water splitting process that also includes OER. Unlike HER, OER involves the transfer of four electrons and additional intermediate conversions. Due to its sluggish kinetics, OER requires higher overpotentials, which diminishes the efficiency of the electrolyzer and escalates the overall cost[10,11]. Therefore, the practical deployment of water splitting significantly relies on the development of highly efficient OER catalysts. Numerous transition metal compounds, including oxides, oxyhydroxides, chalcogenides, phosphides, and nitrides, have been extensively investigated. Strategies such as defect induction, high-performance phase and facet engineering, and developing composite materials have been employed to enhance their intrinsic properties[49-53]. The exploration of active sites based on these methods has contributed to a comprehensive understanding of the reaction dynamics.
Ni(OH)2 nanosheets with two phases, i.e., α and β, show excellent performance for OER. However, the α-Ni(OH)2 can be transferred to γ-NiOOH with improved activity when the anode is overcharged
Figure 3. (A) TEM, enlarged TEM, and HRTEM images for α-Ni(OH)2 hollow spheres, respectively. Inset in (C) shows the corresponding SAED pattern. TEM, enlarged TEM, and HRTEM images for β-Ni(OH)2 nanoplates, respectively. Inset in (F) shows the corresponding SAED pattern. Copyright 2014, American Chemical Society[49]. (B) Impact of facets on the OER activity descriptor. Inset, eg occupancy of six- and seven-coordinated configurations. Reproduced with permission. Copyright 2018, Wiley-VCH[53]. (C) Synthesis schematic of AuSA-MnFeCoNiCu LDH. (D) EDS elemental mapping of Mn, Fe, Co, Ni, Cu, O, Au. The scale bar is 1 μm (E) Projected density of states (EF: Fermi level, εO-2p: O 2p band center) (F) Schematic band diagrams. (G) Computed free energies (ΔG) of OER steps on AuSA-MnFeCoNiCuOOH and MnFeCoNiCuOOH. Copyright 2023, The Authors, published by Springer Nature[63]. UHB: Upper Hubbard band; LHB: lower Hubbard band; N(e): state density.
Doping or multi-metal compounds also show excellent performance for the synergistic effect from different metal sites based on transition metals. High-entropy LDH is limited by the poor stability due to the loss of Fe, resulting in the phase transformation and structure failure. FeCoW oxyhydroxide shows appropriate intermediate adsorption energy with low η10 at 223 mV and 500 h stability[62]. High-entropy LDH
Other compounds, for example, chalcogenides[50], phosphides[66], and nitrides[67], also show good potential for future use in industrial applications. Most of these reports illustrate that these phosphides and nitrides will in situ form metal oxide crystals in the OER process, which serve as the active species for the surface reactions. However, these catalysts exhibit their values as the precursor for the OER. Note that the activity of electrocatalysts of OER relies heavily on the morphologies, size, surface defects, exposure of active sites, disordered structures and grain boundaries that can be induced by the in situ generated metal oxides.
Despite considerable efforts, there remain unclear and imprecise concerns about these materials. Long-term stability and insights into industrial operational conditions are seldom explored. Additionally, the impact of anion atoms, such as O, S, Se, Te, N, and P, remains unclear. Precisely controlling nanocrystal synthesis to obtain the different facets remains a great challenge. Fundamental research employing operando characterizations and simulations has proven effective in identifying high-performance catalysts and enhancing understanding of structure degradation and active sites in catalysts.
HER catalysts
Pt group metals show the best performance of HER in alkaline or acid environments. However, the high cost limits the large-scale application. In alkaline water splitting, the non-noble metals-based materials are generally used both in anodes and cathodes. Great efforts and achievements have been made to develop new non-noble metal materials in recent years. The Ni metal is used in industrial utilization. Its different morphologies with diverse electrochemical surface areas show distinct activities[68-70]. Additionally, the Ni-based alloy is also studied. Ni-Mo can provide the active sites for overcoming the large kinetics energy barrier of the Volmer step with the η10 at 15 mV and exhibit excellent stability [Figure 4A][71]. The synergistic effect of these two metals optimizes the intermediate adsorption energy. Doping non-metal elements such as N and S can enhance the surface area, be in favor of H* adsorption energy and distort the Ni lattice structure thus improving the performance[72]. Besides, CoSn[73], NiCo[74], NiIn[75], NiMoCo[76] and CuTi[77] alloy all show excellent HER performance in alkaline. The enhanced performance can be attributed to the abundant active sites, modulated surface morphology and changed electronic structures.
Figure 4. (A) Calculated free energies of H2O adsorption, activated H2O adsorption, OH adsorption and H adsorption. Copyright 2017, The Authors, published by Springer Nature[71]. (B) Non-volatile solid carbon precursors (for example, CNT) may have different impacts on the chemical composition and microstructure of the carburization product. Copyright 2016, The Authors, published by Springer Nature[79]. (C) Comparison of the overpotentials required at 10 mA cm-2 among our catalyst and available reported HER catalysts. (D) Comparison of the current densities delivered at -200 mV among our catalyst and available reported HER catalysts. Copyright 2018, The Authors, published by Springer Nature[94].
For the transition metal-based compounds, carbides, sulfides and phosphides have attracted much attention. These compounds show adjustable properties. For example, the electronic structure of Mo2C bears similarities to the d-band center of Pt metal, leading to comparable performances[78]. In carbides, the metal is typically the active site. To expose more metal-terminated surfaces, ultrasmall W2C nanoparticles have been synthesized [Figure 4B][79]. However, the costly preparation of carbides remains a significant challenge for their applications. Phosphides can significantly change the conductivity, corrosion resistance and electronic structures. Some strategies for improving OER were also adopted to optimize the performance of these HER catalysts. Fe-doped Ni2P shows η500 at 100 mV[80]. CoP nanoparticles[81,82], Co2P nanorods[83], V-Ni5P4[84] and P-Fe3O4[85] all show alkaline HER performance. Nevertheless, the synthesis of phosphides typically involves the high-temperature decomposition of inorganic phosphorus sources, resulting in the toxic PH3. Safe and facile synthesis methods need to be developed. Chalcogenides, including sulfides and selenides such as MoS2[86], MoSe2[87], CoS2[88] and FeS2[89], have been extensively studied using various strategies[84-87]. Metal doping and anion doping have both shown the ability to enhance performance, albeit through different mechanisms. Metal doping reduces electron transfer resistance, while anion doping significantly alters the crystal structure, modifies active sites, or optimizes reaction kinetics[88-91].
Another strategy to improve the performance effectively is to fabricate the heterostructure with different materials. Carbon materials are useful for serving as electronic conductors. For example, the NiO/Ni-carbon nanotube (CNT) has η10 of about 80 mV. NiO can facilitate water dissociation and OH- adsorption, while Ni promotes the combination of hydrogen atoms to form hydrogen molecules[92]. Co/N-carbon shows a comparable performance with Pt[93]. FeP/NiP requires η10 of about 14 mV, which is a bifunctional catalyst for both HER and OER in alkaline [Figure 4C and D][94]. CoP/Ni2P requires a low η10 of about 16 mV because of the optimized hydrogen adsorption strength. The heterostructure can protect the active materials, resulting in improved stability[95].
The exact factor for the sluggish kinetics of HER in alkaline environment is still unclear. Different mechanisms are proposed to interpret the reaction process under various conditions. For industrial applications, the good stability and high current density in corrosive electrolytes are still insufficient. Transition metal-based materials are economically suitable for HER, but they easily experience structure failure during the reaction, resulting in a deterioration in performance. Moreover, preparing materials such as the above-mentioned phosphides requires harsh conditions, which also should be further optimized.
OPERATION CONDITIONS
In industrial operation, four critical operational parameters are considered, including current density, temperature, pressure, and water quality. Conventional current density typically falls within the range of 200 to 400 mA cm-2. Increased current densities can expedite electrochemical reaction rates, but they come with elevated investment requirements. Moreover, the rapid formation of bubbles at higher current densities can lead to heightened overpotential due to increased resistance caused by these bubbles. Striking a balance between cost and efficiency is pivotal in determining the optimal current density[11,39].
Temperature and pressure significantly influence the electrolysis efficiency for hydrogen production. The water splitting reaction, occurring at the equilibrium voltage of 1.23 V at 1 bar and 25 °C, is endothermic, and the thermoneutral voltage is 1.48 V. Considering that electricity is a higher value than heat, raising the operating temperature with a lower operating voltage can reduce cost. As shown in Figure 5A, the equilibrium voltage is greatly influenced by the operating temperature, which means heat exchange between the cell and the environment is a critical consideration[39]. Moreover, cell temperature notably influences the overall cell voltage during high-rate operation from the following two key factors: the decrease in polarizations at the anode and cathode [Figure 5B] and alterations in the ionic conductivity of the electrolyte. Additionally, the intrinsic properties of diaphragms change with increasing temperature. For example, the resistivity of commonly used 0.5 mm thick Zirfon diaphragms in alkaline water splitting decreases from 4 Ω·cm at 30 °C to 2 Ω·cm at 80 °C. Operating pressure primarily affects efficiency by altering the behavior of gas bubbles[39]. Gas bubbles are particularly sensitive to pressure during high-rate operations (502 mA cm-2). Increasing pressure from 1 to 15 bar results in a consistent decrease in cell voltage, whereas at pressures higher than 15 bar, the cell voltage fluctuates within a small range. The notable decrease in voltage occurs at pressures below 15 bar, likely due to the pressure (up to 35 bar) reducing the size of bubbles, thereby minimizing resistance from bubble overpotential[39]. Gas impurity changes due to increased pressure and temperature slightly influence these processes. Oxygen diffusion and permeation, resulting from electrolyte cross-permeation, contribute significantly to increased hydrogen impurity. The oxygen diffusion coefficient increases and dominates gas crossover despite decreased solubility when raising the operating temperature.
Figure 5. (A) Equilibrium and thermoneutral voltages for water electrolysis as a function of temperature. (B) Schematic structures of an electrolytic cell, gap electrode assembly, and zero-gap electrode assembly. Copyright 2018, American Chemical Society[39]. (C) Engineering electrocatalysts for direct seawater electrolysis. Protocols for cathode modification of electronic structure modulation, tailoring local environment, and interface engineering. (D) Protocols for anode modification of building protective layer, tailoring local environment, and building Cl- repulsion layer.
Gas impurity is an important indicator in industrial applications, especially in alkaline electrolyzers. Permeation demonstrates a significant reliance on supersaturation. However, the overall crossover is predominantly influenced by electrolyte cycling, attributing to approximately 90% at 0.7 A cm-2 and 1 bar. Implementing electrolyzers with separated cycles can help manage this concern. For safety reasons, it is vital to ensure that the highest concentration of hydrogen in oxygen gas does not exceed 2 vol.%. Hydrogen permeation across the separation unit is over ten times smaller, mainly due to the considerably lower hydrogen solubility in concentrated KOH electrolytes, as discussed previously. Additionally, decreased current density and rising system pressure lead to the dissolution of gases, thus increasing the gas impurity. Therefore, low pressure and a high current density are recommended to generate high-purity hydrogen[39].
The water quality is another critical factor that strongly influences both efficiency and stability in electrocatalytic hydrogen production. These impurities may react with the species in the electrolyte, which could diminish Faradaic efficiency (FE), lead to undesired side reactions, and possibly escalate operational costs[44]. Additionally, impurities may accumulate within the system over time, leading to increased cleaning costs and reduced operational efficiency. Therefore, to extend the longevity of applications, regularly replenishing fresh water helps compensate for water consumption. Moreover, impurity metal salts deposited on electrodes can have varied effects, either positively or negatively, on the performance of catalysts. One potential approach to address this challenge involves utilizing catalyst immobilization based on self-assembled and self-healing films, which could aid in mitigating the effects of impurities on the system[11].
ALKALINE SEAWATER SPLITTING
Alkaline water splitting is a mature technology for large-scale hydrogen production. Great efforts made in this field aim to increase the efficiency and reduce the cost. However, it relies heavily on the freshwater supply. The pretreatment of fresh water can be costly[96]. Moreover, building green hydrogen factories in arid areas can be a challenge due to freshwater scarcity. Therefore, large-scale electrolysis projects need more sustainable and flexible solutions. Many offshore and coastal renewable energy plants have been established.
High salinity, pH fluctuations, and complex composition of seawater pose significant hurdles for direct electrolysis. The intricate mix of inorganic salts, organic molecules, microplastics, living organisms, and dissolved gases can deactivate catalysts, electrodes, or membranes[97]. The low ionic concentration of seawater leads to increased energy consumption, rendering the process economically inefficient. The precipitation of compounds such as Mg(OH)2 and Ca(OH)2 blocks electrodes, degrading active sites for essential reactions[98]. Moreover, the oxidation of chloride ions in seawater will compete with OER and related products will corrode the non-noble metal catalysts, leading to catalyst deterioration. Alkaline seawater splitting is a more attractive and promising approach. Some methods can modulate the electrocatalysis through the functional design of catalysts and electrolytes, as shown in Figure 5C and D[14]. Some transition metal-based nitrides have unique electronic structures and anticorrosive properties. The local environment can be adjusted by inducing a Lewis acid layer, which can dynamically split water, capture hydroxyl anions and facilitate the HER activity. Some interfaces allow strong electron interaction and prevent the corrosion of Cl-. During OER, chloride oxidation is the competition reaction. Therefore, building the highly selective OER surface on the catalysts is an effective way to enhance the selectivity and activity via a permeable layer stopping the transport of Cl-. Similar to HER, the local environment can be of paramount importance for the OER. Some strong-proton-adsorption materials can facilitate water dissociation requiring lower overpotential. Cl- repulsion layers can be built on the catalyst surface, which can help exclude the chloride oxidation and show superior OER. However, alkaline seawater splitting is still limited by the above-mentioned issues, which makes it far from industrial application[14].
CONCLUSION AND OUTLOOKS
This review discussed different methods for producing large-scale clean hydrogen electrolyzers. The advantages and disadvantages of these electrolyzers were summarized and compared. Among them, AWE has been commercialized for several decades and shows successful applications, theories, experiences, and strategies to enhance our comprehension of this domain, bolstering energy conversion efficiency, and diminishing costs. However, significant room persists for improving the AWE efficiency. PEM exhibits great efficiency with expensive catalysts and membranes. Overall, recent advancements in applications, methodologies, and material engineering technologies have surfaced, introducing novel possibilities in this realm. Despite these advancements, several knowledge gaps remain to be addressed.
The sluggish kinetics of alkaline water splitting remain complex due to multiple factors. For example, the specific local environment, surface active sites, and dynamic nanostructure alterations significantly dictate the mechanism of alkaline water splitting. Therefore, more attention should be paid to modifying active sites, electronic structures, and nanostructures to enhance the intrinsic properties for improved performance.
Electrocatalyst failure in long-term, high-rate alkaline water splitting continues to be ambiguous. The stability requires more systematic and long-term study. Prevalent stability tests conducted using CV, chronopotentiometry, or chronoamperometry in laboratory settings fall short of simulating the prolonged stability required for extensive utilization over thousands of hours in large-scale applications. The high current density and corrosive electrolyte may lead to the reconstruction and microstructure collapse. Hash operation conditions, such as higher temperature, pressure, and flowing electrolyte, can cause the catalysts to peel off from the electrode surface. Moreover, the detachment of gas bubbles from the electrode surface triggers substantial disturbances in the electrolyte, potentially dislodging catalysts, leading to structural failure and catalyst spalling.
Diverging from controlled laboratory experiments, industrial-scale production encounters more complex challenges and conditions. Factors such as the long distance between anodes and cathodes, bubble accumulation on electrodes, and atmospheric CO2 induced alterations in the electrolyte composition can elevate cell resistance, impeding efficient electron transport. Addressing these issues necessitates the strategic design of cell configurations. Unfortunately, the literature on enhancing these factors in industrial applications is limited, warranting further research and insights in this domain.
Advancements in separator technology are crucial for curbing gas crossover, enhancing ionic conductivity, and ensuring stability in highly corrosive electrolyte environments. This necessity spans both the separator requirements for AEM electrolyzers and conventional alkaline water splitting methods. In the case of AEM electrolyzers, the separator holds exceptional significance. However, current separators face limitations in terms of inadequate conductivity, limited stability in alkaline conditions, and high production costs, particularly inhibiting their large-scale implementation. Efforts in developing high-performance separators seek to address these critical issues and unlock the full potential of these systems.
To simulate industrial production, some new approaches should be considered in the lab. For example, industrial production usually uses different cells, as illustrated in the preceding section. Smaller but similar cell structures should be involved in the lab research to mimic large-scale production. Besides the cell configuration, operation conditions, separator and electrolyte are strongly recommended for most similar experiments with industrial applications. For one specific problem, for instance, bubble management, different electrode models can be developed. Long-term stability research is time-consuming. Calculation simulation can be possibly an effective approach.
DECLARATIONS
Authors’ contributions
Substantial contributions to the conception and design of the study and paper drafting: Zhang Y
Draft discussion and revision: Yao D
Conceived the concept: Liu J
Contributed to the conception and organization of the manuscript and paper revision: Wang Z
Conceived the concept and supervised the whole project: Wang L
Availability of data and materials
Not applicable.
Financial support and sponsorship
The authors would like to acknowledge the support of the Australian Research Council through its DECRA (DE210100930), Discovery (DP200101900, DP200100159, DP230100462) and Laureate Fellowship (FL190100139, FL210100017) schemes. They would also like to acknowledge the support from HBIS-UQ Center for Sustainable Steel and the GrapheneX via the UQ Early Career Researcher Development: Knowledge Exchange & Translation (Kx&T) Fund.
Conflicts of interests
Wang L is an Editorial Board Member of the journal Microstructures. The other authors declare that there are no conflicts of interest.
Ethical approval and consent to participate
Not applicable.
Consent for publication
Not applicable.
Copyright
© The Author(s) 2024.
REFERENCES
1. Jin H, Xu J, Liu H, et al. Emerging materials and technologies for electrocatalytic seawater splitting. Sci Adv 2023;9:eadi7755.
2. Xu J, Jin H, Lu T, et al. IrOx·nH2O with lattice water-assisted oxygen exchange for high-performance proton exchange membrane water electrolyzers. Sci Adv 2023;9:eadh1718.
3. Xia B, He B, Zhang J, et al. TiO2/FePS3 S-scheme heterojunction for greatly raised photocatalytic hydrogen evolution. Adv Energy Mater 2022;12:2201449.
4. Zhang Y, Yao D, Xia B, Jaroniec M, Ran J, Qiao S. Photocatalytic CO2 reduction: identification and elimination of false-positive results. ACS Energy Lett 2022;7:1611-7.
5. Zhang Y, Zhi X, Harmer JR, et al. Facet-specific active surface regulation of BixMOy (M=Mo, V, W) Nanosheets for boosted photocatalytic CO2 reduction. Angew Chem Int Ed 2022;61:e202212355.
6. Zhang Y, Johannessen B, Zhang P, Gong J, Ran J, Qiao SZ. Reversed electron transfer in dual single atom catalyst for boosted photoreduction of CO2. Adv Mater 2023;35:e2306923.
7. Xia B, Yang Y, Zhang Y, et al. Metal-organic framework with atomically dispersed Ni-N4 sites for greatly-raised visible-light photocatalytic H2 production. Chem Eng J 2022;431:133944.
8. Zhang Q, Zhang TT, Li FY, Xu L. Pompon-like NiCo2O4 nanospheres: a potential candidate for the counter electrode in quantum dot-sensitized solar cells. Tungsten 2023;5:235-46.
9. Yu LH, Tao X, Feng SR, et al. Recent development of three-dimension printed graphene oxide and MXene-based energy storage devices. Tungsten 2024;6:196-211.
10. Wang X, Zheng Y, Sheng W, Xu ZJ, Jaroniec M, Qiao S. Strategies for design of electrocatalysts for hydrogen evolution under alkaline conditions. Mater Today 2020;36:125-38.
11. Kou T, Wang S, Li Y. Perspective on high-rate alkaline water splitting. ACS Mater Lett 2021;3:224-34.
12. Ifkovits ZP, Evans JM, Meier MC, Papadantonakis KM, Lewis NS. Decoupled electrochemical water-splitting systems: a review and perspective. Energy Environ Sci 2021;14:4740-59.
13. Hu C, Zhang L, Gong J. Recent progress made in the mechanism comprehension and design of electrocatalysts for alkaline water splitting. Energy Environ Sci 2019;12:2620-45.
14. Yu ZY, Duan Y, Feng XY, Yu X, Gao MR, Yu SH. Clean and affordable hydrogen fuel from alkaline water splitting: past, recent progress, and future prospects. Adv Mater 2021;33:2007100.
15. Clean Hydrogen Market. Available from: https://www.precedenceresearch.com/clean-hydrogen-market [Last accessed on 7 Apr 2024].
16. Zahra R, Pervaiz E, Yang M, et al. A review on nickel cobalt sulphide and their hybrids: earth abundant, pH stable electro-catalyst for hydrogen evolution reaction. Int J Hydrogen Energy 2020;45:24518-43.
17. Yao D, Zhang Y, Zhang S, Wan J, Yu H, Jin H. Hybrid water electrolysis with integrated and cascading reactions using two-dimensional electrocatalysts. J Mater Chem A 2023;11:16433-57.
18. Xia B, Zhang Y, Shi B, Ran J, Davey K, Qiao S. Photocatalysts for hydrogen evolution coupled with production of value-added chemicals. Small Methods 2020;4:2000063.
19. Chi J, Jiang Z, Yan J, et al. Recent advancements in bismuth vanadate photoanodes for photoelectrochemical water splitting. Mater Today Chem 2022;26:101060.
20. Xiao M, Wang Z, Maeda K, Liu G, Wang L. Addressing the stability challenge of photo(electro)catalysts towards solar water splitting. Chem Sci 2023;14:3415-27.
21. Liu N, Liu Y, Liu Y, Li Y, Cheng Y, Li H. Modulation of photogenerated holes for enhanced photoelectrocatalytic performance. Microstructures 2023;3:2023001.
22. Pan JB, Wang BH, Shen S, Chen L, Yin SF. Introducing bidirectional axial coordination into BiVO4 @metal phthalocyanine core-shell photoanodes for efficient water oxidation. Angew Chem Int Ed 2023;62:202307246.
23. Zeng K, Zhang D. Recent progress in alkaline water electrolysis for hydrogen production and applications. Prog Energy Combust Sci 2010;36:307-26.
24. Falcão DS, Pinto AMFR. A review on PEM electrolyzer modelling: guidelines for beginners. J Clean Prod 2020;261:121184.
25. Nechache A, Hody S. Alternative and innovative solid oxide electrolysis cell materials: a short review. Renew Sustain Energy Rev 2021;149:111322.
26. Xiao M, Zhang Y, You J, et al. Addressing the stability challenge of metal halide perovskite based photocatalysts for solar fuel production. J Phys Energy 2022;4:042005.
27. Monny SA, Wang Z, Konarova M, Wang L. Bismuth based photoelectrodes for solar water splitting. J Energy Chem 2021;61:517-30.
28. Zakaria Z, Kamarudin SK. A review of alkaline solid polymer membrane in the application of AEM electrolyzer: materials and characterization. Int J Energy Res 2021;45:18337-54.
29. David M, Ocampo-Martínez C, Sánchez-Peña R. Advances in alkaline water electrolyzers: a review. J Energy Stor 2019;23:392-403.
30. Reier T, Oezaslan M, Strasser P. Electrocatalytic oxygen evolution reaction (OER) on Ru, Ir, and Pt catalysts: a comparative study of nanoparticles and bulk materials. ACS Catal 2012;2:1765-72.
31. Forgie R, Bugosh G, Neyerlin KC, Liu Z, Strasser P. Bimetallic Ru electrocatalysts for the OER and electrolytic water splitting in acidic media. Electrochem Solid-State Lett 2010;13:B36.
32. Danilovic N, Subbaraman R, Chang KC, et al. Using surface segregation to design stable Ru-Ir oxides for the oxygen evolution reaction in acidic environments. Angew Chem Int Ed 2014;53:14016-21.
33. Zheng J, Sheng W, Zhuang Z, Xu B, Yan Y. Universal dependence of hydrogen oxidation and evolution reaction activity of platinum-group metals on pH and hydrogen binding energy. Sci Adv 2016;2:e1501602.
34. Hansen JN, Prats H, Toudahl KK, et al. Is there anything better than Pt for HER? ACS Energy Lett 2021;6:1175-80.
35. Kraglund MR, Carmo M, Schiller G, et al. Ion-solvating membranes as a new approach towards high rate alkaline electrolyzers. Energy Environ Sci 2019;12:3313-8.
36. Hodges A, Hoang AL, Tsekouras G, et al. A high-performance capillary-fed electrolysis cell promises more cost-competitive renewable hydrogen. Nat Commun 2022;13:1304.
37. Park S, Liu L, Demirkır Ç, et al. Solutal marangoni effect determines bubble dynamics during electrocatalytic hydrogen evolution. Nat Chem 2023;15:1532-40.
38. Xu Q, Liang L, Nie T, She Y, Tao L, Guo L. Effect of electrolyte pH on oxygen bubble behavior in photoelectrochemical water splitting. J Phys Chem C 2023;127:5308-20.
39. Ju W, Heinz MVF, Pusterla L, et al. Lab-scale alkaline water electrolyzer for bridging material fundamentals with realistic operation. ACS Sustain Chem Eng 2018;6:4829-37.
40. Kou T, Wang S, Shi R, et al. Periodic porous 3D electrodes mitigate gas bubble traffic during alkaline water electrolysis at high current densities. Adv Energy Mater 2020;10:2002955.
41. Schalenbach M, Kasian O, Mayrhofer KJ. An alkaline water electrolyzer with nickel electrodes enables efficient high current density operation. Int J Hydrogen Energy 2018;43:11932-8.
42. Schalenbach M, Zeradjanin AR, Kasian O, Cherevko S, Mayrhofer KJ. A perspective on low-temperature water electrolysis - challenges in alkaline and acidic technology. Int J Electrochem Sci 2018;13:1173-226.
43. Shinagawa T, Takanabe K. Towards versatile and sustainable hydrogen production through electrocatalytic water splitting: electrolyte engineering. ChemSusChem 2017;10:1318-36.
44. Chung DY, Lopes PP, Farinazzo Bergamo Dias Martins P, et al. Dynamic stability of active sites in hydr(oxy)oxides for the oxygen evolution reaction. Nat Energy 2020;5:222-30.
45. Renaud R, Leroy RL. Separator materials for use in alkaline water electrolysers. Int J Hydrogen Energy 1982;7:155-66.
46. Lee JW, Lee C, Lee JH, et al. Cerium oxide-polysulfone composite separator for an advanced alkaline electrolyzer. Polymers 2020;12:2821.
47. Brauns J, Schönebeck J, Kraglund MR, et al. Evaluation of diaphragms and membranes as separators for alkaline water electrolysis. J Electrochem Soc 2021;168:014510.
48. Zhao X, He D, Xia BY, Sun Y, You B. Ambient electrosynthesis toward single-atom sites for electrocatalytic green hydrogen cycling. Adv Mater 2023;35:e2210703.
49. Gao M, Sheng W, Zhuang Z, et al. Efficient water oxidation using nanostructured α-nickel-hydroxide as an electrocatalyst. J Am Chem Soc 2014;136:7077-84.
50. Gao Q, Huang CQ, Ju YM, et al. Phase-selective syntheses of cobalt telluride nanofleeces for efficient oxygen evolution catalysts. Angew Chem Int Ed 2017;56:7769-73.
51. Meng Y, Song W, Huang H, Ren Z, Chen SY, Suib SL. Structure-property relationship of bifunctional MnO2 nanostructures: highly efficient, ultra-stable electrochemical water oxidation and oxygen reduction reaction catalysts identified in alkaline media. J Am Chem Soc 2014;136:11452-64.
52. Smith RDL, Prévot MS, Fagan RD, et al. Photochemical route for accessing amorphous metal oxide materials for water oxidation catalysis. Science 2013;340:60-3.
53. Wu H, Yang T, Du Y, Shen L, Ho GW. Identification of facet-governing reactivity in hematite for oxygen evolution. Adv Mater 2018;30:e1804341.
54. Feng LL, Yu G, Wu Y, et al. High-index faceted Ni3S2 nanosheet arrays as highly active and ultrastable electrocatalysts for water splitting. J Am Chem Soc 2015;137:14023-6.
55. Li XX, Liu XC, Liu C, Zeng JM, Qi XP. Co3O4/stainless steel catalyst with synergistic effect of oxygen vacancies and phosphorus doping for overall water splitting. Tungsten 2023;5:100-8.
56. Xu L, Jiang Q, Xiao Z, et al. Plasma-engraved Co3O4 nanosheets with oxygen vacancies and high surface area for the oxygen evolution reaction. Angew Chem Int Ed 2016;128:5363-7.
57. Ling T, Yan DY, Jiao Y, et al. Engineering surface atomic structure of single-crystal cobalt (II) oxide nanorods for superior electrocatalysis. Nat Commun 2016;7:12876.
58. Wu YJ, Yang J, Tu TX, et al. Evolution of cationic vacancy defects: a motif for surface restructuration of OER precatalyst. Angew Chem Int Ed 2021;60:26829-36.
59. Yu ZY, Duan Y, Liu JD, et al. Unconventional CN vacancies suppress iron-leaching in Prussian blue analogue pre-catalyst for boosted oxygen evolution catalysis. Nat Commun 2019;10:2799.
60. Chen G, Zhu Y, Chen HM, et al. An amorphous nickel-iron-based electrocatalyst with unusual local structures for ultrafast oxygen evolution reaction. Adv Mater 2019;31:e1900883.
61. Liu Y, Liang X, Gu L, et al. Corrosion engineering towards efficient oxygen evolution electrodes with stable catalytic activity for over 6000 hours. Nat Commun 2018;9:2609.
62. Zhang B, Zheng X, Voznyy O, et al. Homogeneously dispersed multimetal oxygen-evolving catalysts. Science 2016;352:333-7.
63. Wang F, Zou P, Zhang Y, et al. Activating lattice oxygen in high-entropy LDH for robust and durable water oxidation. Nat Commun 2023;14:6019.
64. Nguyen TX, Tsai CC, Nguyen VT, et al. High entropy promoted active site in layered double hydroxide for ultra-stable oxygen evolution reaction electrocatalyst. Chem Eng J 2023;466:143352.
65. Ding Y, Wang Z, Liang Z, et al. A monolayer high-entropy layered hydroxide frame for efficient oxygen evolution reaction. Adv Mater 2023:2302860.
66. Ryu J, Jung N, Jang JH, Kim H, Yoo SJ. In situ transformation of hydrogen-evolving CoP nanoparticles: toward efficient oxygen evolution catalysts bearing dispersed morphologies with Co-oxo/hydroxo molecular units. ACS Catal 2015;5:4066-74.
67. Chen P, Xu K, Fang Z, et al. Metallic Co4N porous nanowire arrays activated by surface oxidation as electrocatalysts for the oxygen evolution reaction. Angew Chem Int Ed 2015;127:14923-7.
68. Ahn SH, Hwang SJ, Yoo SJ, et al. Electrodeposited Ni dendrites with high activity and durability for hydrogen evolution reaction in alkaline water electrolysis. J Mater Chem 2012;22:15153.
69. Kim M, Kim J, Qin L, Mathew S, Han Y, Li OL. Gas-liquid interfacial plasma engineering under dilute nitric acid to improve hydrophilicity and OER performance of nickel foam. Prog Nat Sci Mater Int 2022;32:608-16.
70. Zhang Y, Teng X, Ma Z, Wang R, Lau W, Shan A. Cu2O-templated fabrication of Ni(OH)2·0.75H2O hollow tubes for electrocatalytic oxygen evolution reaction. Prog Nat Sci Mater Int 2022;32:554-60.
71. Zhang J, Wang T, Liu P, et al. Efficient hydrogen production on MoNi4 electrocatalysts with fast water dissociation kinetics. Nat Commun 2017;8:15437.
72. Li Y, Tan X, Chen S, et al. Processable surface modification of nickel-heteroatom (N, S) Bridge sites for promoted alkaline hydrogen evolution. Angew Chem Int Ed 2019;58:461-6.
73. Menezes PW, Panda C, Garai S, Walter C, Guiet A, Driess M. Structurally ordered intermetallic cobalt stannide nanocrystals for high-performance electrocatalytic overall water-splitting. Angew Chem Int Ed 2018;130:15457-62.
74. Hong SH, Ahn SH, Choi I, et al. Fabrication and evaluation of nickel cobalt alloy electrocatalysts for alkaline water splitting. Appl Sur Sci 2014;307:146-52.
75. Mondal S, Dutta S, Mal S, Pati SK, Bhattacharyya S. Lattice mismatch guided nickel-indium heterogeneous alloy electrocatalysts for promoting the alkaline hydrogen evolution. Angew Chem Int Ed 2023;62:e202301269.
76. Mao F, Wang ZG, Cheng L, et al. Electrodeposited multimetal alloyed NiMoCo on Ni mesh for efficient alkaline hydrogen evolution reaction. Energy Fuels 2023;37:18137-44.
77. Lu Q, Hutchings GS, Yu W, et al. Highly porous non-precious bimetallic electrocatalysts for efficient hydrogen evolution. Nat Commun 2015;6:6567.
78. Kitchin JR, Nørskov JK, Barteau MA, Chen JG. Trends in the chemical properties of early transition metal carbide surfaces: a density functional study. Catal Today 2005;105:66-73.
79. Gong Q, Wang Y, Hu Q, et al. Ultrasmall and phase-pure W2C nanoparticles for efficient electrocatalytic and photoelectrochemical hydrogen evolution. Nat Commun 2016;7:13216.
80. Li H, Li L, Li Y. The electronic structure and geometric structure of nanoclusters as catalytic active sites. Nanotechnol Rev 2013;2:515-28.
81. Tabassum H, Guo W, Meng W, et al. Metal-organic frameworks derived cobalt phosphide architecture encapsulated into B/N co-doped graphene nanotubes for all pH value electrochemical hydrogen evolution. Adv Energy Mater 2017;7:1601671.
82. Yang F, Chen Y, Cheng G, Chen S, Luo W. Ultrathin nitrogen-doped carbon coated with CoP for efficient hydrogen evolution. ACS Catal 2017;7:3824-31.
83. Huang Z, Chen Z, Chen Z, Lv C, Humphrey MG, Zhang C. Cobalt phosphide nanorods as an efficient electrocatalyst for the hydrogen evolution reaction. Nano Energy 2014;9:373-82.
84. Rao Y, Wang S, Zhang R, et al. Nanoporous V-Doped Ni5P4 microsphere: a highly efficient electrocatalyst for hydrogen evolution reaction at all pH. ACS Appl Mater Interfaces 2020;12:37092-9.
85. Zhang J, Shang X, Ren H, et al. Modulation of inverse spinel Fe3O4 by phosphorus doping as an industrially promising electrocatalyst for hydrogen evolution. Adv Mater 2019;31:e1905107.
86. Wiensch JD, John J, Velazquez JM, et al. Comparative study in acidic and alkaline media of the effects of pH and crystallinity on the hydrogen-evolution reaction on MoS2 and MoSe2. ACS Energy Lett 2017;2:2234-8.
87. Yan Y, Xia B, Xu Z, Wang X. Recent development of molybdenum sulfides as advanced electrocatalysts for hydrogen evolution reaction. ACS Catal 2014;4:1693-705.
88. Hao J, Yang W, Peng Z, Zhang C, Huang Z, Shi W. A nitrogen doping method for CoS2 electrocatalysts with enhanced water oxidation performance. ACS Catal 2017;7:4214-20.
89. Miao R, Dutta B, Sahoo S, et al. Mesoporous iron sulfide for highly efficient electrocatalytic hydrogen evolution. J Am Chem Soc 2017;139:13604-7.
90. Zheng YR, Wu P, Gao MR, et al. Doping-induced structural phase transition in cobalt diselenide enables enhanced hydrogen evolution catalysis. Nat Commun 2018;9:2533.
91. Yin J, Jin J, Zhang H, et al. Atomic arrangement in metal-doped NiS2 boosts the hydrogen evolution reaction in alkaline media. Angew Chem Int Ed 2019;131:18849-55.
92. Gong M, Zhou W, Tsai MC, et al. Nanoscale nickel oxide/nickel heterostructures for active hydrogen evolution electrocatalysis. Nat Commun 2014;5:4695.
93. Zou X, Huang X, Goswami A, et al. Cobalt-embedded nitrogen-rich carbon nanotubes efficiently catalyze hydrogen evolution reaction at all pH values. Angew Chem Int Ed 2014;126:4461-5.
94. Yu F, Zhou H, Huang Y, et al. High-performance bifunctional porous non-noble metal phosphide catalyst for overall water splitting. Nat Commun 2018;9:2551.
95. Jin M, Zhang X, Shi R, et al. Hierarchical CoP@Ni2P catalysts for pH-universal hydrogen evolution at high current density. Appl Catal B Environ 2021;296:120350.
96. Jin H, Wang X, Tang C, et al. Stable and highly efficient hydrogen evolution from seawater enabled by an unsaturated nickel surface nitride. Adv Mater 2021;33:e2007508.
97. Liu H, Shen W, Jin H, et al. High-performance alkaline seawater electrolysis with anomalous chloride promoted oxygen evolution reaction. Angew Chem Int Ed 2023;62:e202311674.
Cite This Article
Export citation file: BibTeX | RIS
OAE Style
Zhang Y, Yao D, Liu J, Wang Z, Wang L. Advancing strategies on green H2 production via water electrocatalysis: bridging the benchtop research with industrial scale-up. Microstructures 2024;4:2024020. http://dx.doi.org/10.20517/microstructures.2023.87
AMA Style
Zhang Y, Yao D, Liu J, Wang Z, Wang L. Advancing strategies on green H2 production via water electrocatalysis: bridging the benchtop research with industrial scale-up. Microstructures. 2024; 4(2): 2024020. http://dx.doi.org/10.20517/microstructures.2023.87
Chicago/Turabian Style
Zhang, Yanzhao, Dazhi Yao, Jinzhe Liu, Zhiliang Wang, Lianzhou Wang. 2024. "Advancing strategies on green H2 production via water electrocatalysis: bridging the benchtop research with industrial scale-up" Microstructures. 4, no.2: 2024020. http://dx.doi.org/10.20517/microstructures.2023.87
ACS Style
Zhang, Y.; Yao D.; Liu J.; Wang Z.; Wang L. Advancing strategies on green H2 production via water electrocatalysis: bridging the benchtop research with industrial scale-up. Microstructures. 2024, 4, 2024020. http://dx.doi.org/10.20517/microstructures.2023.87
About This Article
Special Issue
Copyright
Data & Comments
Data
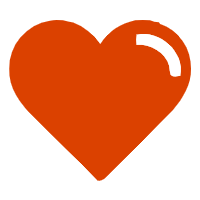

Comments
Comments must be written in English. Spam, offensive content, impersonation, and private information will not be permitted. If any comment is reported and identified as inappropriate content by OAE staff, the comment will be removed without notice. If you have any queries or need any help, please contact us at support@oaepublish.com.